
Elastin is a company in the textile industry, with origins dating back to 1960, and was the first manufacturer of elastic bands in Portugal. The company offers a fast and specialized service in the production of elastic bands for underwear, medical equipment and sportswear, using modern technologies and advanced weaving and dyeing resources, supported by excellent quality control.
The challenge
Elastin was already working with Odoo, in an outdated version, and was looking for a partner that would allow it to have tailor-made developments in order to speed up its processes. Elastin wanted to manage all the company's processes in an integrated way, from the commercial, purchasing and invoicing areas to the logistics and production processes.
The company found the ideal partner in Arxi because of its willingness to find the best solutions for its operational processes, as well as its experience of Odoo implementations in the industrial sector.
The solutions
CRM & Sales
Invoicing
Accounting
Manufacturing
Expenses
Website
Inventory
Maintenance
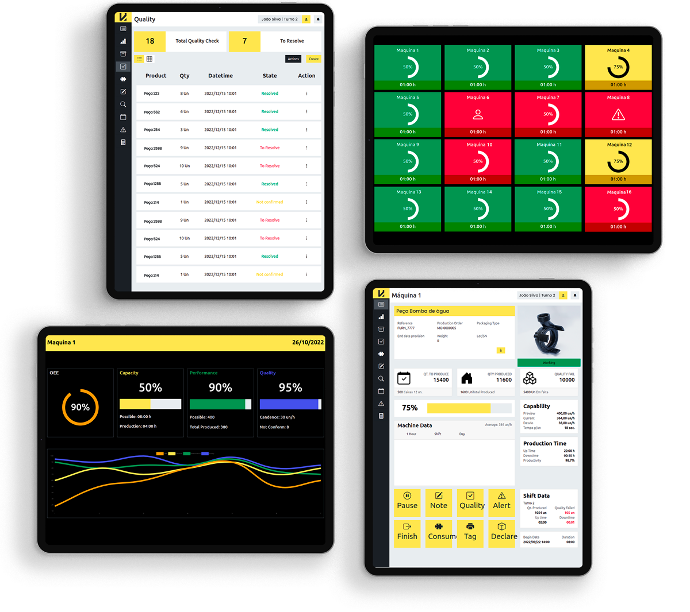
In addition to implementing the business management modules (CRM and Sales, Invoicing, Accounting), Arxi's solution included the tailor-made development of a system of dashboards and screens spread across the shop floor. This system simplified and automated processes that had previously been done manually.
These dashboards and monitors, which are integrated with each other, allow data to be entered at the various stages of production (reception, production, shipments).
Production and warehouse employees punch in their Work Orders, associating them with a specific employee and machine and recording their work and, consequently, the time spent on each task. In these dashboards, employees have access to:
- The product's specifications;
- The bill of materials (BoM);
- The status of the operation, being able to start or suspend it;
- The possibility of writing off articles;
- Creating and printing labels and/or barcodes, as well as work orders.
From a more management-oriented perspective, those responsible for this area also have access to a dashboard with all the Work Order planning - assigned, unassigned, in operation, suspended - and can manage and organize them in a simple way and pull reports that allow them to make strategic decisions based on information about hours spent, materials, resources, etc.
Odoo has thus streamlined all of Elastin's processes, integrating the various departments and production phases and allowing for a more informed analysis of key metrics for optimizing productivity and, consequently, the company's profitability.
Streamline your production today, just like Elastin
Talk to us, without any obligation